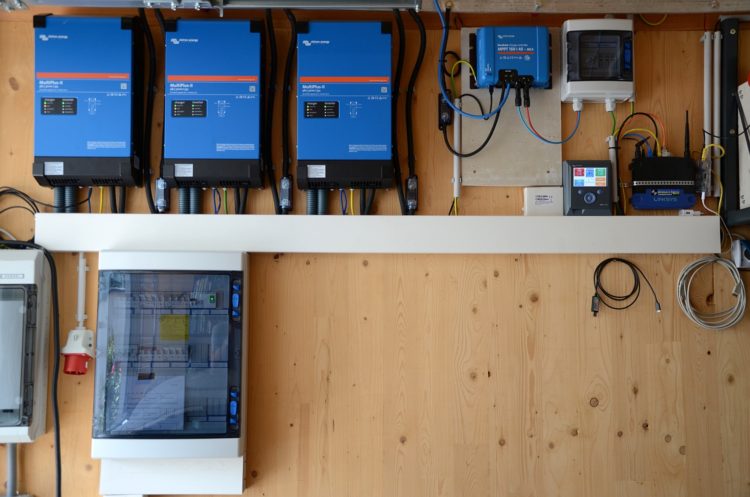
It’s great to hear from Victron Energy customers, be they end users, dealers or indeed budding dealers and installers.
Here’s a case in point. Bernhard Matschinger got in touch with me lauding Victron’s products, which initially led him to build his own PV, Energy Storage UPS system and ultimately his own company – Msol GmbH. For Bernhard this project was a prototype and proof of concept, as it uses non Victron Energy batteries/BMS. That being the case, this gives rise to important safety and system integration considerations. More of that later, but first a bit of history.
Where it all started
Back in 2013, when Bernhard saw his first ‘mjlorton‘ video on YouTube (228K subscribers) he became fascinated by Victron Products. Here’s an example video from that time.
Bernhard is a qualified Civil Engineer with 25 years experience in designing/building low energy homes and industrial buildings. Having been the CTO of a construction company for many years he also made his IT hobby into a profession too, around 10 years ago. So now he has two strings to his bow – one in design and construction, the other creating software based on C#, .Net for Web and ERP.
Due to his experience it was natural for him to want his own PV, Energy Storage & UPS system – so he built one.
System background
Eight years ago Bernhard and his wife built their own low energy family home from scratch, doing nearly all the work themselves.
The area of their home is 255 m², which per annum requires around 2,300 kWh of electricity (6.3 kWh/day), plus 2,600 kWh (7.12kWh/day) for hot water – giving a total of 13.42 kWh/day of electrical energy needs. For space heating they use around 500 kg of wood pellets per annum.
The resulting direct energy costs are around 100 € for heating per year, 260 € for hot water (5 persons) and about 320 € / year for grid energy. That equates to about 1.86 € per day for heat and electricity – significantly less than their neighbours in the region. However when the family got a Tesla Model S, energy usage increased somewhat.
With these increased energy needs and since building their home, Bernhard had always been looking for some grid independence, with ways to reduce direct energy costs, plus a route to ensure no power blackouts.
Standalone PV made little sense, as in the day the family is mostly away from home when excess solar power is available, plus feeding back to the grid pays peanuts at 3.9 cents per kWh. Everything changed though when he discovered Victron products – a result of lots of YouTube research, website surfing, drawings, calculations and finally discovering the Victron MultiPlus – one of his favourite bits of kit that has just what he needs.
Time for some shopping
The primary shopping list:
- 3 x MultiPlus-II
- 1 x BlueSolar 150/45 MPPT
- 1 x Color Control GX
- 24 x 280 Wp Solar Panels
- 16 x LiFeYPo4 cells 260 Ah
- 1 x SolarEdge 5kW + 18 Optimizer
- 1 x Active BMS by AutarcTech
The build
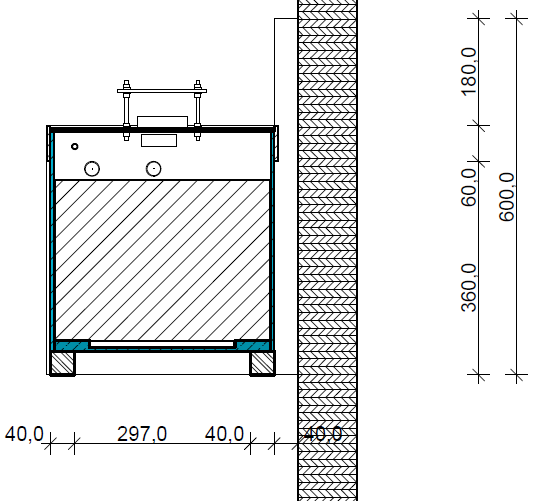
The battery housing is made of 6 mm Promatect (a fire resistant material) which is designed for 60 min fire resistance.
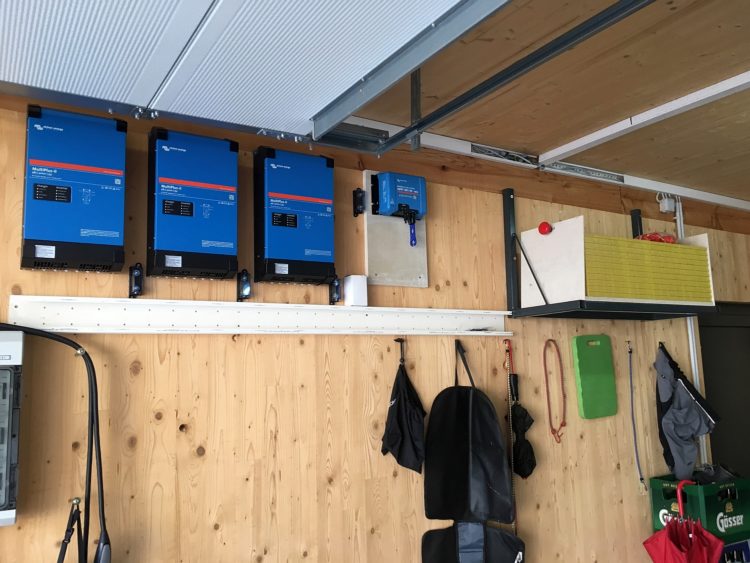
Mounting the Multis, cable trunking and starting to create the fire-resistant housing and rack for the battery cells.
Safety & system integration considerations
With many people now wishing to use second-life batteries (Tesla for example) or indeed new individual cells made into a self-build battery bank, as Berhnard has done – it is very important to be aware of the safety considerations when integrating Victron Energy power products with non Victron batteries and a non Victron supported BMS.
Prior to publishing this blog, we wanted to be certain Bernhard had catered for key safety aspects with his choice of battery/cells – so, we asked:
“Can you confirm if you have installed a safety contactor between the battery and the rest of system, and how that is switched?”
Bernhard responded:
“It is absolutely independent, and yes, there are all breaks on the positive side. The negative side is connected to the common negative pole and is not switchable; all fusing (also the CCGX, the MPPT and the 3 x MultiPlus-II) is done on the positive side. There is a 200A Fuse inside the Battery housing, a manual Contactor (Emergency Switch) and an automatic Relay Contact, driven by the BMS. The cabling is 70 mm² oilflex copper cabling with 3 safety layers.”
“As regards the active BMS by AutarcTech, it monitors each cell for voltage and temperature; plus it monitors the whole bank for max charge and discharge current, over and under voltage and over and under temperature. It also operates the main contactor.”
Bernhard also wrote his own software in Python and C# to collect data from the AutarcTech BMS, to display that data in Visu.
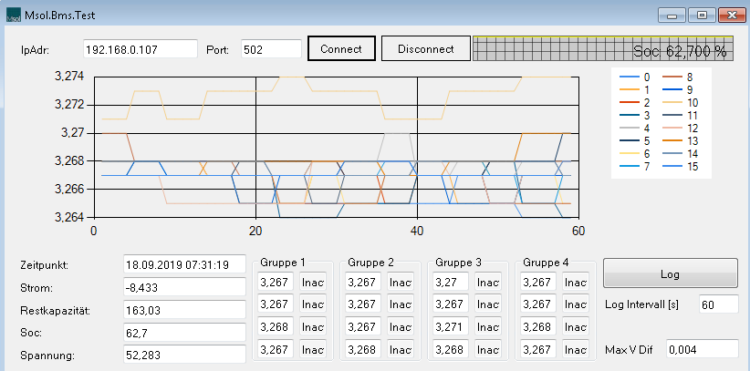
Bernhard’s software, using Visu to display the data for his own personal interest which shows the behaviour of the cells: voltage, charging, discharging or inactive state.
Note: specific information about non Victron, yet compatible batteries that have been tested and are supported can be found here.
Now let’s deal with all the caveats, from a Victron viewpoint, that relate to similar systems to Bernhard’s and integration with Victron products.
Victron Energy safety & liability statement
Here’s what Matthijs Vader, Victron Energy MD had to say:
“To make for a safe lithium system; there must be a mechanism in place that automatically disconnects the battery from the rest of the system on cell under-voltage, over voltage and also on cell-temperature issues as well as other adverse conditions. This means that the voltage on each cell needs to be measured individually. And also temperature needs to be measured and monitored; preferably at cell level, but usually it is also OK to measure it for a certain number of cells together.
Those measurements must be taken care of by a BMS. At Victron we do make BMS-es, but they are only to be used with our own batteries. We do not make general purpose BMS-es. Also, the under voltage lockout of an inverter, and the over voltage protection in a battery charger can *not* substitute a BMS: both only measure total battery voltage, rather than the required individual cell voltages, and temperatures. Finally, the BMS must control a contactor, that disconnects the battery from the rest of the system.
Please take this seriously, any Tesla or other cell over and under voltage can lead to explosive fires and other severe issues.
For which at Victron we take zero responsibility and also accept no liability at all. It’s the responsibility of a BMS to disconnect the battery in case of issues; not of the Victron equipment.
I’d like to help by recommending BMS-es; and I know that at least one company you can consider is REC-BMS: https://www.rec-bms.com/. And I’m sure others active here will have more recommendations.
Lastly, note that there is a distinction between the aggressive chemistries (like in the Tesla cells) and the “safer” LFP chemistry. Definitively for the aggressive ones you need safety measures. The safety risks are less with LFP; but you’d still want one for longevity reasons, and also we do require one / take no responsibility for any safety issues with those either.”
Conclusion
In this project you can clearly see that Bernhard has taken such safety and system integration issues very seriously and his system went successfully live in early April.
From that day on he was able to charge his Tesla and slowly switch the loads to the PV System, once he complied with local planning regulations to connect to the grid. For that he had to hire a professional electrical engineer, who checked the completed system and submitted permit applications to the power company for approval. Now that is completed he has all the required certificates to operate his system in a grid parallel situation.
I think you’ll agree this has turned out a very professional build. Indeed Bernhard is delighted with it and has paid Victron some rather nice compliments too:
- Victron was the best choice I made.
- Wonderful and really good ‘deep diving’ documentation.
- Robust hardware and good supply.
- It all works really well.
Of course having such a neat system, many of his neighbours and others have now shown interest in a system like Bernhard’s. If you have too, why not check out the links below.
My thanks to Bernhard Matschinger of Msol GmbH for the images and information used in this blog.
If you are considering a similar system, don’t forget the Victron Energy Community is a great place to meet fellow Victron users and Victron experts.
John Rushworth
Links
Msol GmbH Website – https://www.msol.at
Msol GmbH on Facebook