
Accepting the challenge to race between the Australian cities of Darwin and Adelaide on public roads using solar power this autumn the UK’s Durham University’s Solar Car Challenge Team are pitching their engineering genius against the world.
The 3000km (around 1870 miles) Bridgestone World Solar Challenge takes place every two years. Vehicles begin the race with 5kWh of stored energy and recharge their lithium batteries as they drive using a shell mounted 4m² (5m² for the ‘Cruiser Class’) solar array.
For over twenty years Durham University’s fifty-strong Department of Engineering team has been designing and building innovation for solar powered vehicles. Their work on aerodynamics, for example, has resulted in a shell so slippery it produces similar drag to the wing mirrors of a conventional car.
Kevlar and Carbon fibre composite has been used for the protective cell which surrounds the driver – ensuring safety in the event of an incident. The team has produced a cell wall material which is as strong as steel, but as light as polystyrene!
On the all-important question of propulsion, in-wheel electric motors using ultra-slim magnets and windings improves efficiency by delivering more torque for less weight. And because direct-drive in-wheel motors eliminate the need for a drive train, less energy is lost to friction, and yet more weight is saved.
The Durham University Solar Car team recently revealed their hand-built and very slick-looking Solar Vehicle in advance of packing it up for the long journey to Australia in a shipping container, which will also act as the vehicle’s mobile race-workshop.
The mobile workshop’s power tools allow for some serious vehicle maintenance on the road – even when that road runs through thousands of miles of wilderness.
Similar mobile workshops closer to home are routinely provided with battery-based power to meet any load – even three-phase loads. Some mobile engineers spend their whole lives helping clients on the road – you can see examples of their rigs here.
The solar race team’s workshop energy demands are modest and highly transportable – even to the other side of the world.
Their container deploys roof mounted solar panels; a SmartSolar MPPT 100|15 solar charge controller harvests energy for storage in a 200Ah lead acid battery. There’s an 800W inverter. Battery state-of-charge, time remaining, usage history – even the battery voltage! – can be read directly from the display of the BMV 712 Smart battery monitor which also has Bluetooth on board, further allowing it to be read from a smartphone or other device via the VictronConnect app.
Road-legal
In addition to engineering innovation, a great deal of testing is conducted in order to prove the vehicle is road-safe with regard to visibility, stability, steering, braking, emergency egress, lighting etc.
Weight reduction is essential for energy saving but brings its own safety-related problems. During the 2019 event crosswinds caused six vehicles to leave the road.
Energy is provided principally by the solar panels, though recovered energy from regenerative braking or whilst travelling downhill is also permissible under race rules. This year’s event restricts the LiFePO4 battery storage allowable cell mass to 36 kg.
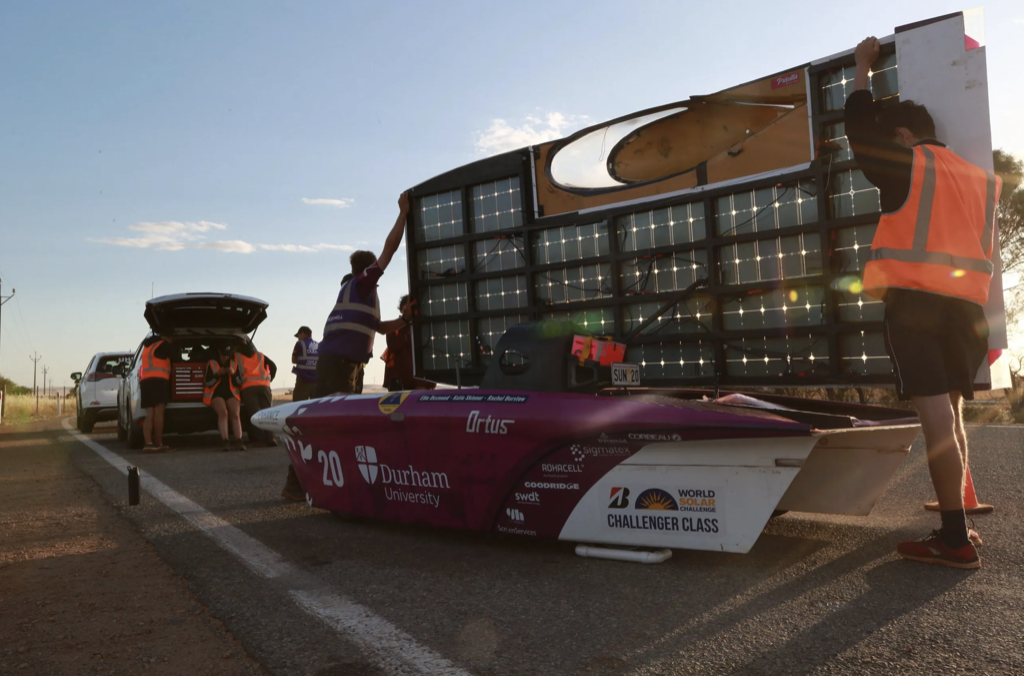
Bridgestone World Solar Challenge
The aim of the Bridgestone World Solar Challenge is to stimulate research into, and development of, sustainable road transport.
There are three classes of entry:
- The Challenger class is a single seat vehicle whose objective is purely speed. The winner will be the first vehicle over the line who has obeyed all rules.
- In the Cruiser class vehicles have a minimum of two seats – accommodating the driver and at least one passenger. The winner is determined by a number of factors including the finish time, but also the amount of energy used (kWh) to achieve their result.
- There is also an Adventure class which is non-competitive, but is an opportunity to try out vehicles which do not meet all the criteria for race entry.
Racing takes place from 0800 until 1700 on each race day, and no sprayed water is permitted for panel-cooling through Australia’s desert environment.
Vehicles are expected to maintain a speed of at least 60kph (just under 40mph) with the course stage timings allowing for an average 75kph (almost 50mph).
Each team is required to rosta between 3 and 6 drivers for their vehicle. It’s not an advantage to choose the lightest members of the team as drivers because each driver will be ballasted to provide 80 kilograms of vehicle-burden.
The Durham University Solar Car
The Durham University Solar Car Team 2023 will ship the car around the world in a container, which is also our support trailer – we will use it to move the car between races, and to follow it during races to provide technical and mechanical support. The support trailer is designed to perfectly fit in a container, allowing us to carry the maximum amount of equipment, whilst also making shipping as easy as possible.
The Victron MPPT is used in the trailer to keep our battery bank charged from the roof-mounted solar panels. This allows us to run our tools off the battery, allowing for constant maintenance of the car, even in the middle of the outback.
Commenting on the solar programme’s benefit for the University as a whole, Ben says: The Durham University Solar Car project is a student led team, comprising of 50 students from all different degree courses. It allows the students to develop their skills in a real world environment, with a common goal, and a shared ambition to win.