
This week let’s hear from ABYC certified marine installer Owen Murphy.
Owen is currently voyaging aboard his 34 foot sailing boat.
Working on stop-overs, early on in his voyage he was asked to install a mind-boggling power system which would allow the 55 foot sailing yacht Flight Risk to provide itself with autonomous power for long periods, powering anything – across multiple voltage topographies, and also to plug-in to shore power anywhere in the world.
It turned into a three-and-a-half month job, and wasn’t for the faint-hearted. At the end of the story there is a footnote from the owner. Read on!
Flight Risk – By Owen Murphy
The immense fuselage of Flight Risk sits high up on the hard in the shipyard of Cape Marina. Cabinets, hatches, panels, and furniture are still open or missing as there is still much for the owner to refit. Bits of teak trim and insulation lie about amongst the internal wreckage that is now a mix of old and shiny new. After originally gutting her circulatory system of every locatable wire, the burden of the task ahead admittedly did intimidate and challenge me. But now after a whole lot of sweat, ripped pants, several miles of electrical vessel carefully woven back into her, and installing nearly every form of marine electrical mechanization, I feel comfortable enough to say that she looks rather stunning, at least from my trade-perspective.
Blinking chargers, humming inverters, brainy modules, controllers, converters, digital panels, analog panels, shunts, finger friendly switches, VHF radios, outlets, plugs, and touch screens galore animate the heart of the vessel. A platoon of lithium ion phosphate batteries, (eight to be exact) are stacked tactically inside to bank the incoming and outgoing electrons. There are so many speakers that one could directly configure sound to every exterior and interior crewman whilst they were napping, working, steering, star gazing, or showering. Two HVAC (Heating Ventilation and Air Conditioning) units and three air handlers for the temperature sensitive mate. Three thaw-proof fridges and freezers, an arctic grade desalination system, an alternator so powerful we removed the ship’s generator, and a European chef-approved convection oven. Accent lighting for that mood, courtesy lighting for guests who might be in a mood, two heads (toilets) that make your household one seem boring, and pumps! Oh yes, pumps of all size and shape for engine oils, fuels, fresh water, salt water, bilge water, you name we can pump it! Not a drop of liquid moves throughout Flight Risk without being punched onward by some electron driven diaphragm or impeller engineered by the most corrosion proof synthetics available.
An octet of fore and aft underwater lights are recessed into the hull for an aquatic theater. Eight powered winches sit about the cockpit to assist in torquing lines for some fourteen-hundred square feet of canvas propulsion. Band windlass lie sleeping as titans ready to manage the nine tons of ballast. A freshly welded stern solar arch flexes two 440 Watt panels but with enough space to also fit a large satellite antenna for high speed interstellar travel via wireless internet. One might check the weather or keep up with their social life all while manning the helm through impending channels and perilous seas. I must not forget to mention that all has been linked and interfaced into an elite ethernet network coinciding with NMEA 2000. Mates can turn on any circuit with the touch of their phone or key fob whilst approaching from dock or dinghy all while drinking their martini. There is more but I fear I might lose the reader if I continue exhausting these little equipment descriptions any further.
When I first spoke to Huffman, the owner of Flight Risk, it was via phone. I was selling second hand Victron LiFePO4 batteries that I had pulled from another vessel during my time employed with Polaris Marine Electrical in Saint Augustine, Florida. I was also about to depart south on my own ship, Rumi a Crealock 34’ Cutter. I’ve been delicately planning my own circumnavigation since I was thirteen years old and my decamping date was in less than a month. Huffman and I hit it off pretty quickly, discussing ships and marine equipment. It wasn’t long before he convinced me to stop through Port Canaveral on my way south to install a complete Victron system and rewire all fifty-five feet of his 1986 Taiwanese built Tayana. I took off on Rumi in early December.
Huffman invited me aboard his ship the same day I pulled into my slip at Cape Marina. “This used to be a really beautiful boat”, he laughed as we climbed below deck. I was immediately met by the growl of an overworked angle grinder and clouds of fiberglass. The engine room bulkheads and stringers were being disemboweled and rebuilt with carbon fiber by a Slovenian named Rocky, a master of composites who I would soon be working alongside. Huffman showed me about the ship revealing the humongous amount of work ahead of me.
With any electrical overhaul, an electrician must first begin by deciphering the ship owner’s needs. How does the owner plan to use the boat? Appropriately sized battery banks, chargers, inverters, generators, distribution blocks, circuit protection, wire runs, diagrams, and equipment layout can then begin. I had already done much of the design in Saint Augustine prior to arrival but things change constantly and much of the puzzle can hardly be worked out without actually being aboard the project itself. Luckily, this was not Huffman’s first refit. The practice of ship overhaul is actually a bit of an ongoing hobby for him. Well educated in ship systems, he already had an idea of the equipment he wanted and we were thus able to corroborate a plan:
- ● 48V DC LiFePO4 house bank capable of inverting all the power needed for the boat – Huffman client was avid about a 48V bank because he also purchased a cutting edge Integral Alternator which puts out a whopping 9KW but at 48V.
- ● A massive 48V to 12V converter system to step power down power from the batteries to nearly all of the ship’s 12V loads
- ● Charging via 2200W of solar – client was having an arch built on the stern to hold two 440W panels. Three more would be going up once the hard Bimini was constructed.
- ● Installing a 9KW Integral alternator on the engine that would replace the ship’s old generator
- ● 230V 50Hz AC power distribution throughout – running outlets, microwaves, Starlink,washer/dryer, convection over, battery chargers, inverters, air conditioning, heating, etc. – Client spent a lot of time in Europe and 230V AC was his preference for utility and efficiency
- ● 120V 60Hz AC power as a separate circuit that would power another set of outlets for American appliances
- ● A 24V DC battery bank with charging in the bow for windlass and bow thruster
- ● A 12V DC bank that would start the engine, run 8 powerful electric cockpit winches (2 new to be installed), and act as an emergency 12V load bank via parallel switching
- ● A DC to DC charging system that allows the boat owner to charge his electric dinghy directly from the ship’s house bank via plug-in at the stern.
- ● A state of the art marine grade Starlink system with boosters for wireless internet
- ● A complete Victron Energy – Cerbo GX network system
- ● A custom built navigation area that would include all the instrumentation and screens for all of the different systems of the boat in addition to VHF, chart plotter, AIS, etc
- ● Fans along with air intake and exhaust blower systems for cooling the living areas and engineroom
- ● Air conditioning and heating
- ● Two marine heads (toilets)
- ● Four bilge pumps operated via their own dedicated control panel
- ● Fuel transfer and polishing system
- ● LED lighting for both interior and exterior, including 8 powerful underwater lights
- ● Fusion sound system with 7 different zones
- ● Sewage treatment system
- ● An electric piano in the salon
- Digital switching throughout the entire boat via CZONE – a system designed by Mastervolt which would allow the user to switch on and off nearly all 12V circuits, as well as group them, from any touch screen on the boat. The client would be able turn on lights, music, etc from the comfort of any location on Flight Risk.
- In addition, I would be installing a wireless programmable key fob that would allow the owner to access up to 5 different circuits from it.
- I almost forgot…digital push button switches would also be installed throughout the boat, cockpit, stern, and bow. These switches are programmable like the key fob and therefore configurable to work with any CZONE circuit. – all part of the owner’s preference.
To say Huffman was a fan of Victron Energy would be a serious understatement. If Victron made the component, Huffman wanted it. So much so that we even installed blue LED lighting in the machine room to give ambiance to Victron’s signature blue boxes. Eight 24V 200Ah Victron Smart LiFePO4 batteries placed in four series pairs would make up the house bank with some 9,600KW of power. AGM batteries would make up the separate 12V and 24V banks used in starting the engine, running the eight electric winches, bow thruster, and windlass. I laughed at the numerous different voltages Flight Risk would contain. When you add the 230V and 120V systems to the list, the vessel Risk would have five different voltages pushing current throughout the boat, a big jump considering most boats this size average only two or three.
Fitting all the wire into the new built machine room turned out to be the greatest challenge of the ship. It had to look clean and too many wires can often make the process difficult. With our combined brain power we decided that Rocky would construct a few large panels. Each panel would sit off the wall on 3” spacers that provide the space I needed to conceal all the conductors behind the instruments for a more flush and clean look. Entering the machine room would feel like popping the hood of a Ferrari by the time we were through with it.
Often, one of the creative challenges of a rewire this large is coming up with new cable runs that can accommodate for the amount of conductors that have to be installed. Most of the old wire routes were ridiculously indirect or unusable from being sealed up by the original builder. You heard me right, I said sealed up!
Anyone who has worked in the marine industry or even owned a boat is familiar with this completely absurd and traditional practice. A grievance that I imagine goes back to the age of Vikings, we boat technicians are in a constant state of displeasure with builders who carelessly construct ship bodies around equipment with little to no concern for their replacement or serviceability. One in truth has to push the limits of contortionism and spelunking, unafraid to lose skin or scalp, glass fibers knifed into fingernails. We dangle upside down, one arm behind our backs, hose clamps buried in our ribs, into dark voids with live wires and soggy pits of mystery bilge ooze all while tooling with the utmost precision. This is all because serviceability gets a back seat when boats are made. Living space wins over workable space every time. I could most easily rant for another page or more of this maddening modus operandi but I think I will spare the reader my monologue.
With Flight Risk, at least half of the original wiring was sealed into the hull walls behind permanently installed paneling, much of it glassed over. My fish tape was fruitless. We could literally dismantle a major portion of the vessel or come up with new wire routing. Fortunately, I was able to squeeze much of the cabling into the ship’s ceilings, but most of it I had to snake elsewhere. Ships of this size do not have crawl spaces like homes. We technicians are usually left to install wiring, plumbing, and equipment through permanently mounted ship furniture.
On Flight Risk, conductors would snake off into so many three dimensional turns, I could end up using forty or fifty feet of wire to reach a component that was only some fifteen feet away. That might sound like no big deal until one realizes that it is not just one wire to be run, but possibly twenty, fifty, or a hundred through that same shared path. Each loom has to look clean and sharp, properly tied in, protected from chafe, scrutinized for parallel form. DC bundles need to be isolated from AC bundles, consideration for thermal buildup and corrosion has to be carefully accounted for. Proper cable sizing is an absolute must. To top it off, there is my own personal standard, serviceability for the owner or next technician.
Now let us imagine that together we have painstakingly done it all. Fortunately, everything fits. The owner walks in. Impressed, he pauses to think and then asks for the fifth time that week, “Hey, I have an idea for a new appliance, can we add just one more wire?”
Having so many different voltages also presented some challenges. Flight Risk’s new operating voltages are both European and American. Nearly all boats use pass-through power from shore when plugged in. This permits AC power to run appliances directly from the grid. Because my client plans to travel to Europe and the USA, we had to design the system so that shore power would travel directly into a 50A – 48V Skylla that can accept 230V 50hz or 240V 60Hz interchangeably without any issue or manual switching. The Skylla solely charges the 48V bank which then sends power out to everything else. The 8KW-230V Quattro Inverter/Charger, the 1600W-110V Phoenix Inverter, the two different battery chargers that power the 12V and 24V banks, and the six 48V to 12V DC to DC Converters – Orions, which send power to the 12V Panel. Despite this clever engineering, shore power was in fact an auxiliary need. Huffman really plans to run the boat almost purely from the sun and with his state of the art and Integral Alternator.
Three international workers came and left throughout the refit. At one point we had a Romanian, a German, and a Slovenian, all working alongside on different mediums. “You still do not know who the owner is, ya?,” asked Rocky one day, an eyebrow cocked, a fresh cigarette gazing down from his lips and himself smirking whilst pausing from grinding away yet another section of stringer soon to be rebuilt with carbon fiber. It was not unusual to see him grind away for three, sometimes four hours at a time without a break. The guy got a kick from keeping the mystery around Huffman’s background a secret. I knew something had to be up, especially after Huffman purchased a mint condition 1996 Jaguar for me to use during my stay. A form of work truck for this electrical vagabond I suppose. Eventually I learned the backstory of it all from Huffman himself but have been asked to keep those details out of the story for his own privacy.
Meeting fellow workers along the way is an added benefit in this world of complicated electrical configurations. Rocky and I usually had a couple beers at the dock after work and often caught a Space-X launch on its way out to seed the atmosphere with another string of satellites. A tall ex-military Slovenian smoking two packs a day, the diction of a movie villain, loved by his little terrier named Pica always prancing about him – the guy was a real character. His favorite hobby was stringing together sinister narratives and mystery around everything. “Ah yes, she will look most beautiful, at the bottom of the sea”, I heard him say, glancing up at Flight Risk through his own smog. Another time I watched him tell a rocket watching stranger, “Ya know, where I am from I am not used to seeing the rockets go up. Usually we watch them come down.” The observer looked back a little disturbed, unable to see through Rocky’s accent that he was having fun with him. We debated everything from boat design, historical interpretation, to mustache likeability. Eventually I won him out in some topics and he did cleave off his beard for a thick caterpillar mustache.
For a month afterward, whenever I closed my eyes, all I could see was a spaghetti of insulated copper, highly organized, of course. I put three and half months of effort into completing the rewire. Huffman baited me to stay longer but my own ship was calling. I needed to be south to Panama before hurricane season set in. I departed at 9am on a Friday to Stuart, Florida. I was overdue for the next part of this adventure. Leaving Port Canaveral was bitter sweet. I have made friends here at the dock in my little slip and I will miss them. I will miss the BBQ’s and NASA happy hour sessions where we debate islands and boat parts while the rockets fire off just a few miles northeast, thickly vibrating the sunsets and stirring them like a maroon latte.
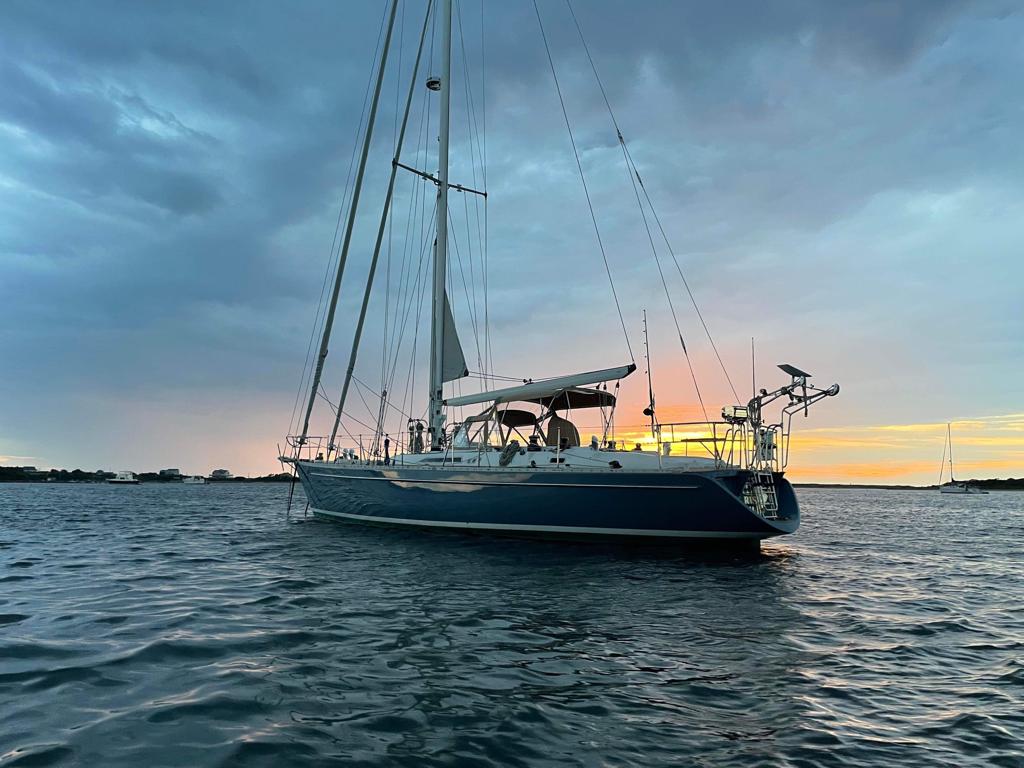
I am very grateful to Huffman, the pilot, sailor, and entrepreneur with a story too big for this blog. I will miss drinking beers and arguing ship design with my Slovenian friend, Rocky, a true living craftsman, tank driver, and persona from a novel somewhere to be written. He even came aboard my boat to try and sell me a gun on his last night in town. I think that the stories of people one meets throughout these little endeavors are often what make all the working parts bearable.
It would have been nice to see Flight Risk completed and in the water before shoving off. However, I know Huffman will be busy for many more months ahead in rebuilding the ship’s interior. As for my part of the gig, I felt content in leaving. I had to sail south.
Owen Murphy is a self taught engineer and shop teacher turned professional marine electrician. He holds an ABYC certification along with thousands of hours in the trade. He sails a fully outfitted 1994 34’ Cutter built by Pacific Seacraft. Currently anchored in Bocas del Toro, Panama, Owen spends his time seeking out life’s little adventures and helping cruisers with their electrical needs in person and remotely along the way. You can follow his progress online at Meridian-Marine-Electrical.com.blog or reach him at owen@meridian-marine-electrical.com
You can also follow his work on Instagram at @meridian-marine-electrical and @owenmurph.
*** Huffman HMH Sailing said that thanks to the equipment from Victron and meticulous system design by Meridian Marine, the 2023 charter season about our Tayana 58 will be nearly carbon neutral. “The mission was to refit an already robust production boat into a true high-latitude vessel for the growing ‘expedition charter’ segment. A veteran Captain of more than 40 years, Schultze says that choosing an integration partner is key to success. Owen at Meridian Marine worked diligently with HMH Sailing to identify energy storage/production needs and expectations in order to design the best possible system for us. “It is a time-consuming process to accomplish correctly, and Owen made it a pleasure. Now, having accomplished our shakedown cruise, seeing everything operate in-service as it was planned has been exciting. How many sailboats can run entire-boat air condition for multiple days from battery power and then recharge in a matter of hours? This is only possible thanks to Victron, Meridian Marine, and Termodinamica.
If you’d like to hear more from Owen talking about electricity and how he fell into his marine power expertise have a listen to him talking to Paul Trammell in this podcast.