BMV-702 head unit together with attachment sleeve. | ||
500A shunt. | ||
Two 1.5m (59") red cables with a 1A fuse. | ||
10m (33ft) RJ12 UTP cable. | ||
Square face plate together with an attachment flange. | ||
Bag with 4 small screws. | ||
Quick installation guide. | ||
Spare serial number sticker. |
The shunt has an IP21 rating; this means that the shunt is not waterproof and has to be mounted in a dry location.
The shunt has two 5.5 mm holes for mounting purposes; these are located in the base of the shunt. The holes can be used to screw or bolt the shunt onto a hard surface (note that these screws are not included).
For the exact location of the mounting holes see the dimension drawing in the appendix of this manual.
Top view shunt indicating mounting holes and side view shunt indicating the mounting method.
The head unit can be mounted in a variety of ways:
Panel mounting, the head unit is secured at the back of a panel.
Panel mounting, the head unit is secured at the front of the panel.
Wall mounting, using an optional wall mounting enclosure.
Mounting method A.
Mounting method B.
Mounting method C.
Note
For the full wall mounting instructions, see the wall mounting installation manuals on the Wall mount enclosure for BMV or MPPT Control or Wall mount enclosure for BMV and Color Control GX product pages.
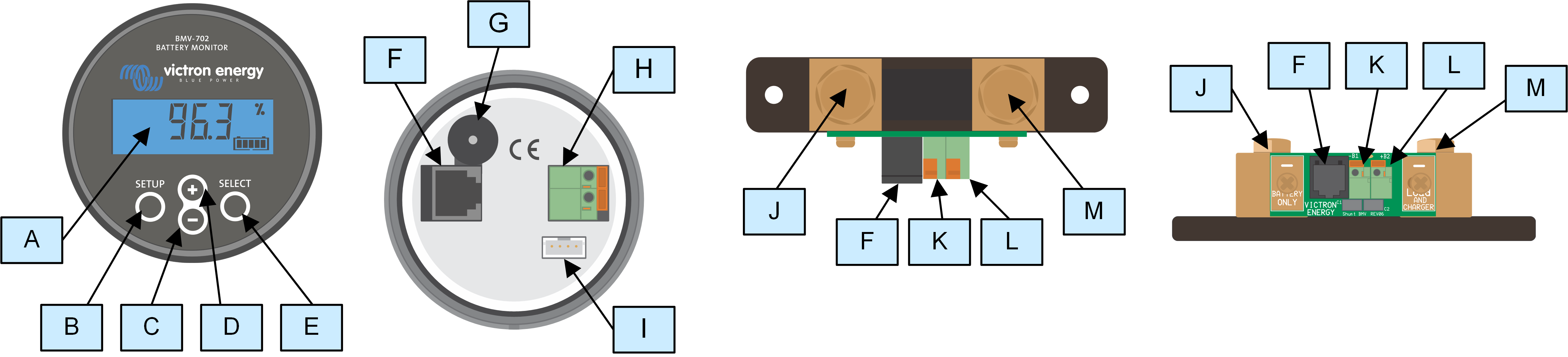
# | Name | Terminal type |
---|---|---|
A | Display | - |
B | Setup button | - |
C | Down button | - |
D | Up button | - |
E | Select button | - |
F | RJ12 connector | RJ2 terminal |
G | Buzzer | - |
H | Programmable relay connector | Push connector |
I | VE.Direct connector | VE.Direct terminal |
J | Negative battery connection | M10 bolt |
K | Positive battery connection | Push connector |
L | Auxilary connection | Push connector |
M | Negative load connection | M10 bolt |
Connection procedure:
Connect the negative battery terminal to the M10 bolt on the "BATTERY ONLY" side of the shunt. Tighten the shunt bolt with a maximum torque of 21Nm.
Note that there should be no other connections on this side of the shunt or on the negative battery terminal. Any loads or chargers connected here will be excluded from the battery state of charge calculation.
Connect the negative of the electrical system to the M10 bolt on the "LOAD AND CHARGER" side of the shunt. Tighten the shunt bolt with a maximum torque of 21Nm. Make sure that the negative of all DC loads, inverters, battery chargers, solar chargers and other charge sources are connected “after” the shunt.
Connect the ferrule pin of the red cable with the fuse to the shunt by pushing the pin into to the “+B1” terminal.
Connect the M10 eye terminal of the red cable with the fuse to the positive terminal of the battery.
Connect the shunt to the head unit using the RJ12 cable. Plug one side of the RJ12 cable into the shunt RJ12 terminal and the other side of the cable into the RJ12 terminal on the rear of the head unit.
The battery monitor is now powered up. The display is active,.
In order to be fully functional, the battery monitor needs to be configured; see the Configuration chapter.
In case the battery monitor is going to be used to monitor a second battery, battery bank midpoint or battery temperature, see one of the next 3 paragraphs on how to do this and then go to the Configuration chapter.
Basic battery monitor installation.
In addition to the comprehensive monitoring of the main battery bank, a second parameter can be monitored. This can be one of the following:
The voltage of a second battery, like a starter battery.
The midpoint deviation of the battery bank.
Battery temperature.
This chapter describes how to wire the +B2 terminal for the three above options.
For use to monitor the voltage of a second battery, such as a starter or auxiliary battery.
Connection procedure:
Verify that the negative pole of the second battery is connected to the LOAD AND CHARGER side of the shunt.
Connect the ferrule pin of the second red cable with fuse to the shunt by pushing the pin into to the +B2 terminal.
Connect the M10 lug of the second red cable with fuse to the positive terminal of the second battery.
Battery monitor with auxiliary second battery monitoring.
For use with a battery bank that consists of multiple batteries that are wired in series or series/parallel to create a 24V or 48V battery bank.
Connection procedure:
Connect the ferrule pin of the second red cable with fuse to the shunt by pushing the pin into to the +B2 terminal.
Connect the M10 lug of the second red cable with fuse to the positive terminal of the midpoint.
For more information on midpoint monitoring and for additional diagrams on midpoint battery bank wiring see the Midpoint voltage monitoring chapter.
Battery monitor with auxiliary midpoint monitoring.
For use to monitor the temperature of a battery via the (not included) Temperature sensor for BMV-712 Smart and BMV-702 . This temperature sensor needs to be purchased separately. Be aware that this is a different temperature sensor than the temperature sensors that are included with Victron inverter/chargers and some battery chargers.
Temperature sensor for the battery monitor
Connection procedure:
Connect the ferrule pin of the black temperature sensor wire by pushing the ferule pin into the +B2 terminal.
Connect the ferrule pin of the red wire cable by pushing the ferule pin into to the +B1 terminal.
Connect the M10 cable lug of the temperature sensor to the positive battery terminal.
Battery monitor with auxiliary temperature sensing.
Note
Note that if the temperature sensor is used, the two red cables with fuse that came with the battery monitor are not needed. The temperature sensor will replace these cables.
The battery monitor is equipped with a programable relay. This relay can be used as an alarm relay, to start a generator or for other applications. For more information on the various relay modes and how to configure the relay, see chapter Relay settings.
A usage example of the relay is to start a generator when the battery state of charge has dropped too low, and then to stop the generator when the batteries have been recharged.
By default, the relay is set to energise when the battery state of charge falls below 50% and to de-energise when the battery state of charge has risen to 90%. However, the relay can be configured to also trigger on other conditions, like battery voltage.
The relay has 2 contacts: COM (common) and NO (normally open) and are located on the back of the head unit.
When the relay contact is open, the coil is de-energised; there is no contact between COM and NO. When the relay is energised, the relay closes, and contact between COM and NO is made. The relay function can be inverted: de-energised becomes energised and vice versa. See setting Invert relay. When the relay is energised, the power consumption of the battery monitor will increase slightly: see the Technical data chapter.
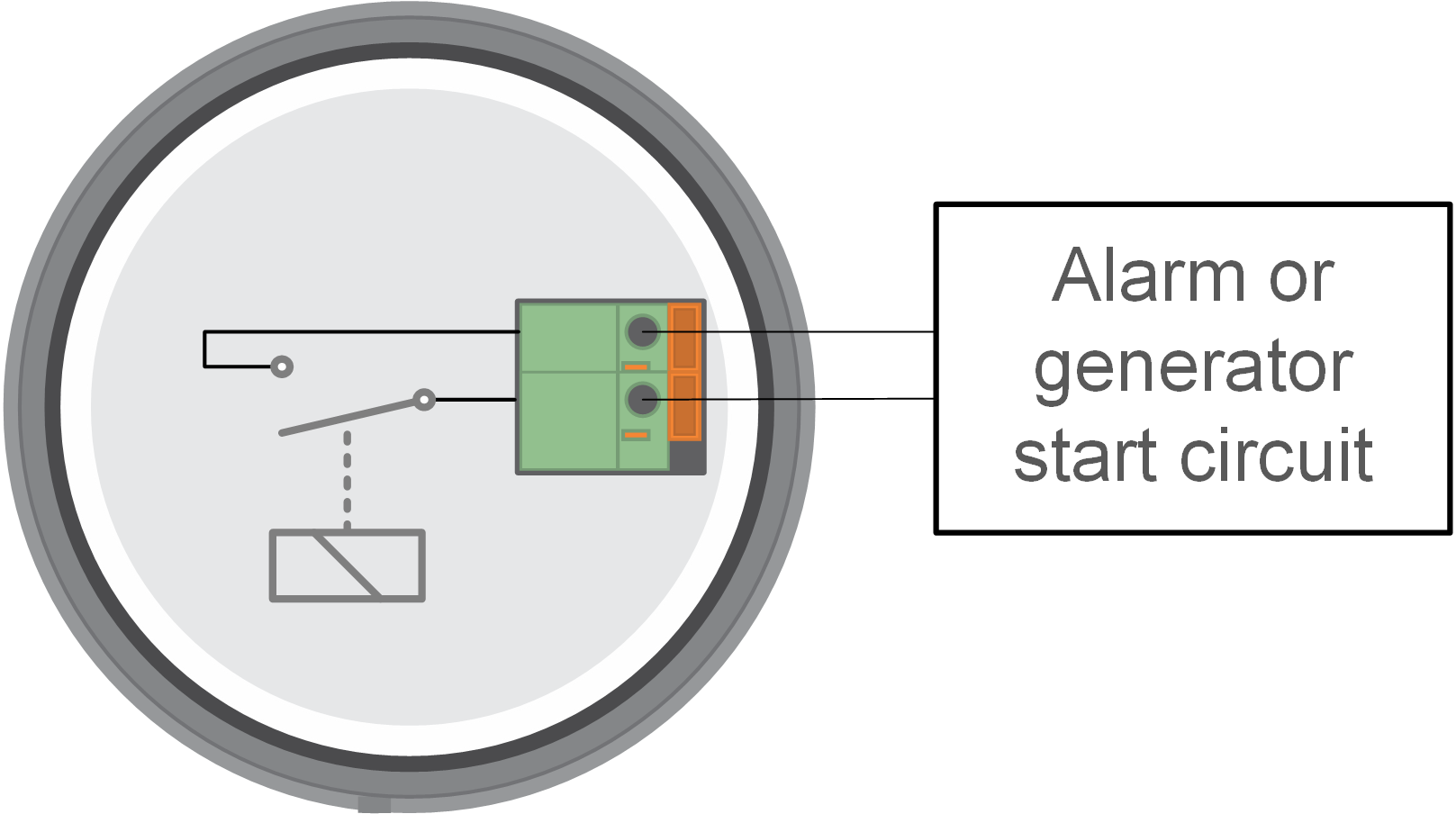
The internal wiring diagram of the battery monitor with the relay in a de-energised state connected to an external alarm or generator start circuit.
The battery monitor is supplied with a 500A, 50mV shunt. This shunt is suitable for most applications. However, a larger shunt will be required if system currents above 500A are expected.
The battery monitor can be configured to work with a wide range of different shunts. Shunts of up to 9999A and up to 75mV can be used. For a selection of larger shunts, i.e. 1000A, 2000A or 6000A, see our shunt product page.
When using a shunt other than the one supplied with the battery monitor, please proceed as follows:
Unscrew the circuit board from the shunt.
Mount the circuit board on the new shunt, and ensure that there is good electrical contact between the circuit board and the shunt.
Connect the new shunt to the electrical system and battery monitor head unit as shown in chapter Basic electrical connections. Pay special attention to the orientation of the shunt circuit board in relation to the battery and load connections.
Follow the setup wizard; see the Setup wizard chapter.
After completing the setup wizard, set the proper shunt current and shunt voltage according to the Shunt current and the Shunt voltage settings.
If the battery monitor reads a non-zero current, even when there is no load, and the battery is not being charged, calibrate the zero current reading using the Zero current calibration setting.
If the system contains a GX device such as a Cerbo GX, the battery monitor can be connected to the GX device using a VE.Direct cable or a VE.Direct to USB interface.
Once connected, the GX device can be used to read out all monitored battery parameters. For more information see chapter Connecting to a GX device and the VRM portal.