The Smart IP43 Charger range is designed to be permanently mounted using the mounting flanges integrated into the heat sink.
Before mounting, the following aspects should be considered to identify/provide a suitable and safe location:
Install the charger in a location with good natural airflow/ventilation; in case airflow is a restricted, consider adding a cooling fan.
Ensure there is sufficient unobstructed space around the charger; a minimum clearance of 100mm above and below is recommended.
Install the charger on a non-flammable substrate and ensure there are no heat-sensitive items in the immediate vicinity; it is normal for the charger to become hot during operation.
Install the charger in a location where it is protected from environmental conditions such as water, high moisture and dust, and also located well away from any flammable liquids or gasses.
Do not install or place/operate the charger on top of the battery, directly above the battery, or in a sealed compartment with the battery; batteries can emit explosive gasses.
Do not cover or place any other items on top of the charger.
Mount the Smart IP43 Charger vertically with the terminals facing down; secure using suitable screws though the mounting holes/slots.
Select and use screws with a pan/flange head (do not use screws with a countersunk/tapered head), and a screw thread outer diameter well matched to the mounting hole/slot internal diameter (~5mm max OD to provide a clearance fit).
To aid installation, it is recommended to 'hang' the unit using the 2 upper screws (leave the screw heads ~3mm from the surface) and then install the 2 lower screws, before fully securing all 4 screws.
Refer to the drawing below for mounting dimensions:
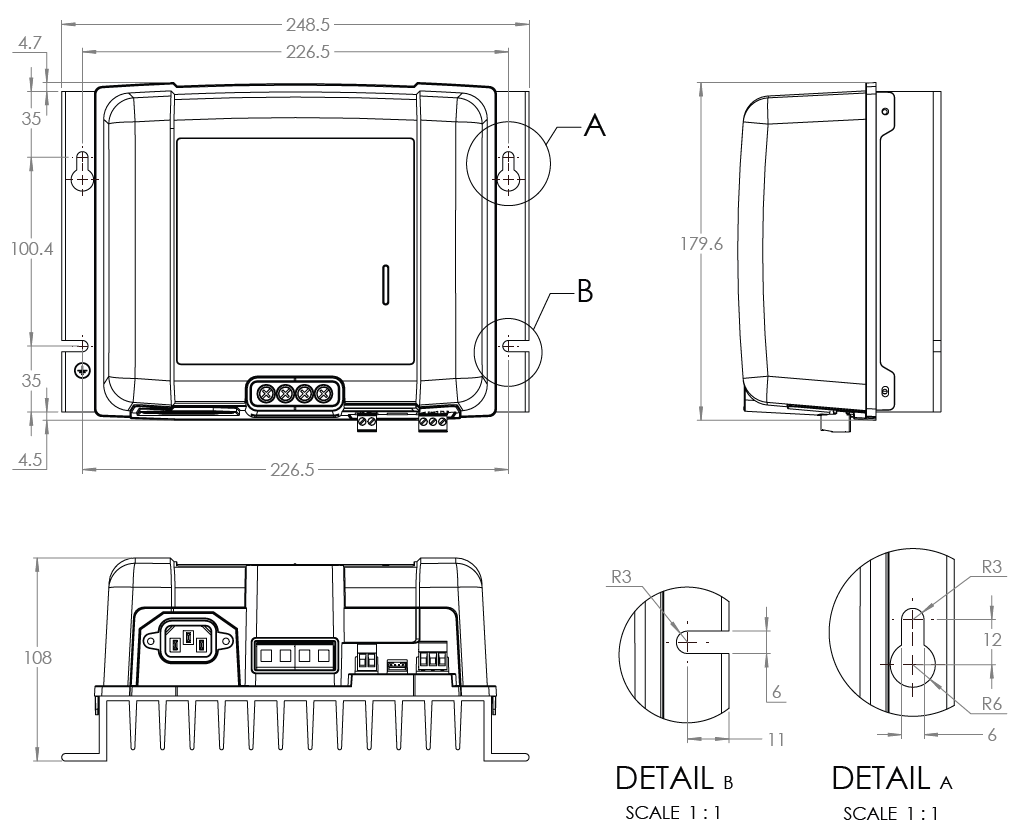
Connect suitable DC power cabling to the Smart IP43 Chargers BATTERY terminals.
Use flexible multi stranded copper DC power cable with sufficient cross sectional area, inline with an appropriate fuse or circuit breaker; refer to the 'Installation > Wiring > DC power cable' and 'Installation > Wiring > Overcurrent protection' sections for more information.
Ensure that wiring polarity is correct; connect the positive DC cable (red insulation) to the positive (+ ) terminal and negative DC cable (black insulation) to the negative (-) terminal connection.
Torque the terminal screws to 2.4Nm using a small torque wrench with a suitable screw driver bit.
Connect the DC power cabling to the battery/batteries or DC system distribution bus - follow the instructions relevant to the installation type.
For fixed installations, or when charging a battery outside of a vehicle/installation:
Ensure that the DC system is shut down (all DC loads and charge sources off/isolated) prior to disconnection of any existing battery / DC system distribution bus cabling and connection of the charger to the battery terminals / DC system distribution bus.
Ensure that wiring polarity is correct; connect the positive DC cable (red insulation) to the positive (+) terminal and negative DC cable (black insulation) to the negative (-) terminal.
Torque all wiring termination hardware to manufacturers torque specifications using a suitable torque wrench and socket / screw driver bit.
For temporary installations when charging a battery installed within a vehicle, and the negative (-) battery terminal is grounded to the vehicle chassis (conventional):
Connect the positive DC cable / battery clamp (red insulation) directly to the battery positive (+) terminal first.
Then connect the negative DC cable / battery clamp (black insulation) to a suitable grounding point on the vehicle chassis (not directly to the negative battery terminal).
When disconnecting the charger, disconnect the DC cables / battery clamps in reverse of the connection order.
For temporary installations when charging a battery installed within a vehicle, and the positive (+) battery terminal is grounded to the vehicle chassis (unconventional):
Connect the negative DC cable / battery clamp (black insulation) directly to the battery negative (-) terminal first.
Then connect the positive DC cable / battery clamp (red insulation) to a suitable grounding point on the vehicle chassis (not directly to the positive battery terminal).
When disconnecting the charger, disconnect the DC cables / battery clamps in reverse of the connection order.
Connect VE.Direct communication cable (between VE.Direct port on charger and Venus device) and/or control wiring (remote on/off and/or programmable relay) as required for the installation.
Connect the AC power cable to a mains power outlet; all LEDs will illuminate briefly when the charger is powered up, then the LEDs indicating the current charge mode and charge state will illuminate.
Notice
Example wiring schematics depicting most typical installation configurations are also provided for reference; refer to the 'Installation > Schematics' section for more information.
To ensure reliable and safe operation it is important to select and install suitably rated DC power cabling between the Smart IP43 Charger and the battery/batteries.
Cable type/specification selection should consider the following aspects:
Conductor material and cross sectional area
Conductor material and cross sectional area effects the resistance of a cable per unit length, and accordingly determines the maximum current capability/rating, as well as the power loss / voltage drop over the total cable length.
To prevent overheating of the cable and/or interfacing equipment, select high quality power cable with copper conductors and a conductor cross sectional area appropriately sized for the application.
The cable manufacturers maximum current rating for the cable (after applying any de-rating factors applicable to the installation) must exceed the maximum operating current possible within the system, and the cable must also be capable to safely withstand the fault current required to blow the fuse / trip the circuit breaker.
To prevent high power loss and operational issues due to excessive voltage drop, design the system layout so that cable lengths are as short as possible and if needed increase conductor cross sectional area to reduce voltage drop to an acceptable level.
If needed, it is recommended to increase conductor cross sectional area so that the voltage drop over the total cable length is below ~0.5V and ~3% at maximum operating current.
Strand diameter
Strand diameter effects the contact area / resistance and accordingly determines the amount heat generated at terminations, as well as the flexibility capability/rating of the cable.
To prevent overheating of the cable and/or interfacing equipment at/near terminations, select high quality power cable with fine multi-stranded copper conductors.
In order to maximise contact area and minimise resistance at terminations, the diameter of each individual copper strand must not exceed 0.4mm (0.016 inch) or a surface area of 0.125mm² (AWG26).
If cable with a thicker strand diameter is used, the contact area at the interface between the conductor strands and termination will be insufficient and cause excessive resistance. A high resistance electrical connection will generate substantial heat when operating under load and result in severe overheating or potentially a fire.
To enable easy cable routing with tight bends and prevent failure of the cable and/or interfacing equipment due to excessive force/stress at terminations and/or cyclic fatigue, select high quality power cable specifically designed for applications requiring high flexibility.
It is recommended to use high quality power cable with a flexibility class rating of 5 or higher (according to VDE 0295, IEC 60228 and BS6360).
Insulation type
Insulation type effects the maximum temperature capability/rating and accordingly the maximum current capability/rating, as well as the maximum voltage isolation capability/rating of a cable.
To prevent overheating of the cable insulation, select high quality power cable with an insulation temperature rating appropriate for the installation.
The cable manufacturers insulation temperature rating must exceed the maximum projected temperature for the installation, when considering the combination of maximum possible surrounding temperature and temperature rise due the heat generated by the cable itself under maximum load.
It is recommended to use high quality power cable with a maximum temperature rating of at least 90°C (194°F).
To ensure robust electrical isolation, select high quality power cable with an insulation voltage rating appropriate for the maximum operating voltage of the system.
It is recommended to use high quality power cable with a maximum voltage rating of 0.6/1kV.
Refer to the table below for the recommended minimum cable cross sectional area / gauge in relation to cable length (one way length between charger and battery):
The Smart IP43 Charger is equipped with remote on/off terminals, these terminals enable charging to be turned on or off remotely dependent on their state.
There are 3 options to turn the Smart IP43 Charger on using the remote terminal(s):
Interconnect / short the L and H terminals (factory default is a shorting link between L and H). The L and H terminal can be interconnected /shorted via a switch, relay or other external device, like a battery management system (BMS).
Pull the H terminal to a high voltage level; when the voltage on the H terminal is above 2.9V (connected to battery positive for example) the charger will turn on. The H terminal can be connected to a high voltage level via a switch, relay or other external device, like a battery management system (BMS).
Pull the L terminal to a low voltage level; when the voltage on the L terminal is below 3.5V (connected to battery negative for example) the charger will turn off. The L terminal can be connected to a low voltage level via a switch, relay or other external device, like a battery management system (BMS).
To turn the Smart IP43 Charger off using the remote terminal(s), both terminals need to have an open circuit relative to each other and be left floating (no connection to a high or low voltage level).
The Smart IP43 Charger is equipped with a programmable relay, the relay can be used for external control based on the selected relay mode (Alarm, Remote control, or Charging) and operational conditions.
There are 3 programmable relay terminals:
NO (Normally open)
C (Common)
NC (Normally closed)
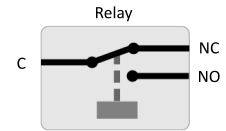
When the relay is switched off there is a closed circuit between C and NC, and an open circuit between C an NO.
When the relay is switched on there is a closed circuit between C and NO, and an open circuit between C an NC.
Wire the relay terminals to an external device as necessary in order to achieve the desired signal/control.
Notice
Note: The programmable relay function only works when AC input power is available and charging is enabled. If charging is disabled by any means (the remote on/off terminals, via VictronConnect or a GX device) the programmable relay functionally will also be disabled.